Do these few simple tasks to avoid the lost production due to nuisance shut-downs. These measures may also recognize the warning signs of and prevent an impending catastrophic failure.
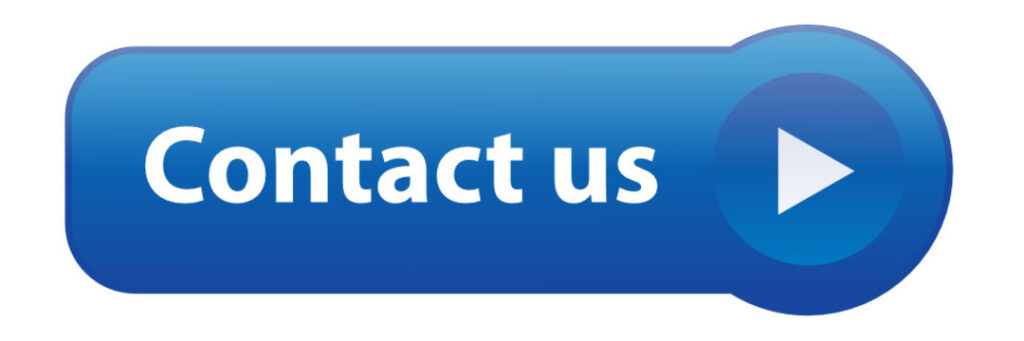
Daily
1). Check oil level. Oil seals the compression area in a rotary screw or a rotary vane compressor or vacuum pump. Oil also lubricates the bearings. The third function that is just as important as the other two is cooling. In fact some manufacturers refer to oil as the coolant.
Weekly
1). Check the oil cooler. If the cooler is the least bit dirty or dusty the efficiency will drop off immediately. Oil operating above 1950F has half the published service life. This includes synthetic oil. If any leaks are found, even small “weeping” leaks, call Air Vac Systems, Inc. immediately for repairs. Small leaks will allow a mist or fog to envelop the cooling fins creating a high temp situation.
2). Check the after-cooler. A dirty after-cooler will result in hotter than specified air entering the dryer, resulting in a high dew point.
Monthly
1). Check the inlet filter for obstructions. Debris blocking the inlet area of the filter housing will result in a higher amp draw as well as higher operating temperatures.
2). Check the drain on the moisture separator for the after-cooler. If a non-functioning or blocked drain is found either perform repairs immediately or call air Vac Systems, Inc. A nonfunctioning drain totally defeats the purpose of an after-cooler. A nonfunctioning drain will allow liquid water to flow directly into the refrigerated or desiccant dryer. In either case the dryer will suffer. A refrigerated dryer pre filter can become saturated, rendering it useless and cause massive pressure drop. The desiccant in a pressure swing dryer will be rendered useless and will require expensive replacement.
3). Check the drain for the moisture trap on the refrigerated dryer. If a nonfunctioning or blocked drain is found either perform re[pairs or immediately call Air Vac Systems, Inc. A nonfunctioning drain will allow liquid water to flow directly into the system causing damage to air bearings, the piping system or any other processes or machinery that demands dry air.
4). Check the drain on the receiver tank. A malfunctioning drain will allow liquid water to accumulate in the receiver, causing premature failure due to pin holes and rust.
Quarterly
Call Air Vac Systems, Inc. to perform an amp draw, thermal mixing valve function test as well as refresh all pressure and flow settings. All pressure relief valves, temperature switches, motor control overloads as well as thermistors or transducers will be tested and adjusted where possible.
Semi-Annually
Keep up with your recommended service interval. Call Air-Vac Systems, Inc. for semi-annual service
Annually
Service your equipment per the manufacturer’s recommendation. Call Air-Vac Systems, Inc. for annual service.