Remember, all compressors are NOT created equal. To demonstrate this point, we will assume you have a 25 horsepower (18 -19 kw) rotary screw air compressor installed. The usual path taken by on-line buyers is to look for the cheapest 25 h.p. screw compressor available, buy it, install it, and start it up. The next thing that usually happens is to wonder why there is low pressure in the system. After all, a 25 h.p. screw compressor replaced a 25 h.p. screw compressor, right?
What could go wrong?
It turns out a LOT can go wrong. There are reasons cheap compressors are cheap. Manufacturing tolerances for one thing. When machine tools wear out or old casting molds are used repeatedly clearances open, gaps get wider, and the overall efficiency of the finished product is compromised. New or sharpened tooling adds to production costs. Replacing worn casting molds add to production costs as well. What all this means is that manufacturing methods in third world countries, where most cheap compressors originate, are usually slipshod when compared to methods utilized in industrialized countries.
Example: 25 h.p. (18.642 k.w.) Puma compressor manufactured in Turkey = 106 cfm @ 108 psig
25 h.p. (18.642 k.w.) Boge compressor manufactured in Germany = 114 cfm @ 110 psig
The 8 cfm difference amounts to, coincidentally, an 8% difference in efficiency. The lower efficiency amounts to several hundred dollars annual increase in energy costs. It also amounts to the inability to operate at least two air tools, depending on the type of tools in question. Less capacity translates directly to lowered production capability resulting in a smaller output for higher production costs. So, where is the savings generated by buying a cheap compressor?
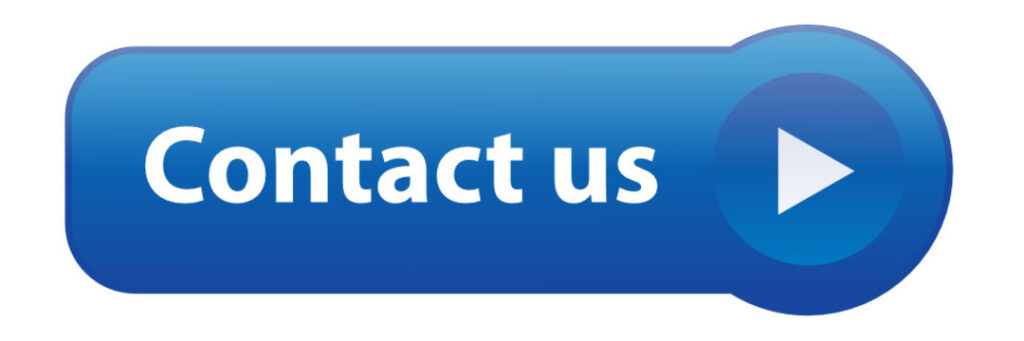
What can be done?
First, check the published capacity of the manufacturer of the machine you are considering. Compare the capacity at the rated pressure against your existing machine. It is very important that the rated pressure be adhered to. A lower pressure will result in a higher capacity. You cannot simply increase the pressure of a new machine. To stay within the design amp draw of an electrical motor, rotation speed against a specific workload is dictated. Try to increase the load (increase pressure) and the unit must decrease speed to stay within operating parameters. When the speed is decreased the flow is reduced. Thus, higher pressure machines deliver less flow.
The next step is to go to the CAGI (Compressed Air and Gas Institute) website, https://www.cagi.org/performance-verification/data-sheets.aspx . The site is intuitive. Find the type of compressor you are considering; find the manufacturer of the unit you want. Look at the performance data sheets for your exact model. If the manufacturer of the unit under consideration is not listed, or the exact model is not listed, don’t consider that unit at all. Chances are if the manufacturer is not listed, they don’t perform as they advertise. If that is the case their new machine will cause you to have low pressure, lost production, lower billing, and a much lower profit margin.
I will give you a real-world illustration of the danger associated with a cheap compressor from a non-industrialized source. We were called early one morning from a company we had never serviced nor had any past transactions with. He demanded we repair a compressor from an unknown (to us) manufacturer. Since we didn’t recognize the brand name, we informed the caller it would be a waste of our time and his money to respond. He then sent us the serial number of the unit and demanded we show up with all the parts to make repairs. In an attempt to help, we Googled the compressor name. It was made in Turkey. There are no parts available in the U.S. His issue was someone had stolen all the copper wire from his control panel. There are no schematics available. No schedule of wire sizes used. Nothing. Yet he claimed we were incompetent because we couldn’t source parts based on the serial number, could not replace the wire without a schematic and so forth. His claim was we just didn’t want to work on his unit because he had avoided being ripped off by the local compressor distributors.
Once the decision has been made that the available machine is in fact reliable and a viable replacement for the existing machine, you must decide whether the new compressor is to be the only one online or is the old unit to be retained as a back-up. Or, as in some cases, is the old unit going to be retained as occasional supplemental air source due to more machinery being added or a change in manufacturing methods. If there is to be two units operating simultaneously there must be adequate electrical service available. Breakers, disconnects, fuses and correctly sized wire and conduit must all be installed. After all, you cannot just plug the new machine into a handy wall outlet. If you are buying a machine online, total responsibility for assuring the electrical service is adequate and in compliance with all applicable local, city, county and state building and electrical codes is all yours. Violate any of these and there may be an issue with your insurance company in the case of a liability claim in the future.
Is the area selected for installation of the new unit correct? Does the area have adequate ventilation to prevent elevated operating temperatures? Is the area free of dust and debris? Does the slab or foundation meet applicable building codes? Are the mounting devices in compliance with any required seismic codes? Is there adequate hazardous material (oil) containment? Are vibration pads or spring isolators required to meet codes or stay in compliance with manufacturer’s warranty requirements?
After the area has been selected, placement is the next consideration. Is there enough room around the machine to allow for routine service? What about major repairs (they will occur, cooler removal, air end overhaul or replacement)? Are there areas around the machine that cause “dead air”, meaning areas where ambient air fails to circulate? These areas can cause elevated operating temperatures as well as allow dust to collect.
Is there an area nearby that will accommodate the installation of a grounding rod? Modern control technology is computer controlled. In addition to a requirement for “clean” and stable electrical supply, efficient grounding is a necessity. In the old days electro-pneumatic controls could get by with reliance on standard building circuitry grounding. Not so now. A positive, uninterrupted ground is an absolute necessity to assure correct, efficient operation as well as protecting incredibly expensive electronic componentry. The cost of a variable frequency drive alone can easily equal 25 to 30% of the total cost of a new machine. The cost of a new motor wound to withstand the stress of variable frequency operation, in some cases, far outstrips the cost of a standard wound motor.
If a refrigerated dryer is installed, is it in the same room as the compressor/s? Will the new compressor coolers add enough additional btu load to raise the ambient air temperature? Will the increase exceed the design parameters of the dryer? If the ambient air temperature is increased the efficiency of the dryer will decrease. This may result in “wet” air.
Will additional receivers be required? Most likely. The correct receiver capacity, in gallons, is 25% above the capacity, in cfm, of the compressor.
A handy formula is multiplying the horsepower of the compressor by (4). Then multiply the result by 1.25.
Example: A 25 h.p. compressor.
25 x 4 = 100 cfm
100 cfm multiplied by 1.25 = 125 gallons required
The closest standard size receiver is 120 gallons This would probably work but ideally the next size up would be preferable. The next larger standard size would be 200 gallons.
Remember, if you are adding a new 25 h.p. compressor to an existing unit, the receiver capacity must be increased to handle both units, not either or.
ALWAYS, always, always exceed the maximum working pressure of the highest pressure compressor in the system. ALWAYS. My rule is to always use a 200-psig working pressure tank in any standard low pressure industrial system. It adds a bit to the cost but there is never any concern about the rated pressure of the tank being exceeded. It also adds to the service life of the tank. A thicker tank shell and heads allow for unavoidable internal corrosion.
You must also size the pressure relief valves correctly. They must be rated below the working pressure of the tank and yet slightly above the rated pressure of the highest-pressure compressor in the network.
Of course, tank drains, drain service valves, gages and system service valves must be selected and installed in the system.
Correct interconnecting piping and filters must be selected, sized, and installed along with a three-valve bypass to allow for service of the filter elements without a complete system shutdown. A system shutdown obviously results in the complete secession of production. Or you can pay overtime for the service taking place outside of regular business hours.
The type of filters will be determined by the air quality required. The service interval will be determined by the size, quality and type filter media selected.
Is the existing oil-water separator of sufficient capacity to accommodate and efficiently treat the increased condensate generated by the additional compressor, dryer, and filters? If not, then this too will require an upgrade.
So, if you are qualified and feel confident making all the above-mentioned decisions then by all means, save a couple hundred dollars and buy your next compressor online. If you feel uncomfortable making these decisions, get a compressed air specialist and make that person assume the responsibility.
Still need help? Contact us today!
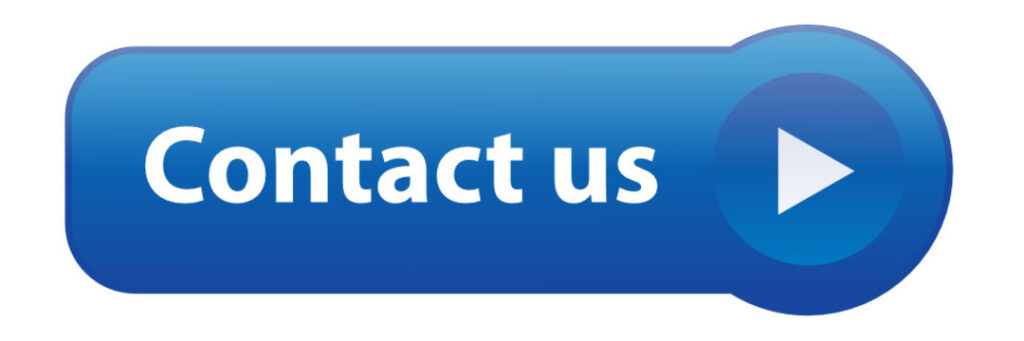